Cement production accounts for roughly 8% of global carbon emissions, and in a milestone step toward adoption and lowering emissions now, materials technology company Fortera has opened its Redding ReCarb® Plant, the first industrial green cement and carbon mineralization facility in North America and one of the largest of its kind in the world. Located in Redding, California, Fortera’s plant will capture carbon dioxide (CO2) emitted during cement production and permanently sequester it by mineralizing the CO2 into ready-to-use cement. Not only will this reduce carbon emissions by 70% on a ton-for-ton basis and eliminate feedstock waste associated with traditional concrete production, but every year, the facility will capture 6,600 tons of CO2 and produce 15,000 tons of low-carbon ReAct® cement. Fortera will integrate with green energy supply at future plants, achieving true zero-CO2 cement.
This press release features multimedia. View the full release here: https://www.businesswire.com/news/home/20240412693182/en/
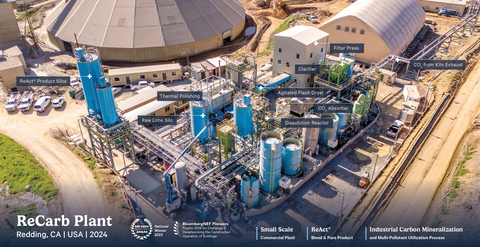
Fortera’s new ReCarb Plant is co-located with CalPortland in Redding, Calif. This first-of-its-kind plant executes Fortera’s patented ReCarb process technology on a commercial scale, while also providing the building and industrial sectors with a scalable solution to reduce carbon emissions. (Photo: Business Wire)
“Redding is the first of many plants in Fortera’s future as a green cement producer, and achieving this milestone brings the industry that much closer to realizing zero-carbon cement, which is critical for both our continued infrastructure and the health of our planet,” said Ryan Gilliam, CEO of Fortera. “While significant, we recognize this is one step in a much larger effort to reach commercialization globally, and we are committed to scaling our technology using existing infrastructure to mobilize widespread adoption of low and zero-carbon cement.”
Fortera’s ReCarb process is a collaborative bolt-on technology that works within existing cement production infrastructure rather than building new stand-alone plants from the ground up, providing a sustainability solution that can be implemented quickly, economically, and efficiently. In Redding, Fortera’s ReCarb facility is adjacent to CalPortland’s cement plant. Fortera captures CO2 emitted during calcination—the process occurring when limestone is heated in a kiln—and draws the gas from CalPortland’s flue gas stack into the ReCarb plant, where it undergoes mineralization to transform the gas into ReAct green cement, a rare form of calcium carbonate.
“For 132 years, CalPortland has developed resilient and sustainable cement and concrete products. We understand the importance of using science-driven research to continue to develop new and innovative products that will have a positive impact on the future,” said Steve Regis, CalPortland Executive Vice President. “We are excited to partner with Fortera at our Redding Cement plant as they develop their new ReCarb technology and congratulate them on the completion of their new facility.”
Since cement is the most significant source of CO2 emissions in concrete production, the ReCarb technology reduces carbon emissions throughout the value chain without imposing substantial capital costs and creates a product that is just as effective as ordinary cement. ReCarb also increases overall product output. When limestone is heated in a kiln to make ordinary cement, nearly half is lost as CO2. Mineralizing those emissions through ReCarb produces a ton of green cement for every ton of limestone feedstock used. Further, ReCarb reduces energy use by using a lower kiln temperature and creates a path to zero CO2 cement when combined with renewable energy.
Following the opening of the Redding ReCarb plant, Fortera will begin producing ReAct green cement, which will be available later this quarter for ready-mix suppliers. ReAct can be used on its own or blended with ordinary cement. It is ASTM-approved, exhibits the same strength and durability as ordinary cement and complies with existing regulations. When blended, ReAct lowers the overall carbon footprint of construction projects while maintaining strength and increasing workability.
The Fortera Redding ReCarb Plant is the culmination of over 100,000 hours of research and development and more than a decade of rigorous testing and real-world product demonstrations. The Net-Zero Industries Awards recently named Fortera the 2023 U.S. National Winner for Outstanding Projects. ReAct is a Green Builder Media 2024 Sustainable Product of the Year.
To learn more about how Fortera is paving a path to zero CO2 cement production, visit forteraglobal.com.
About Fortera
Fortera is a pioneering materials technology company paving the way to zero CO2 cement. Drawing on more than ten years of real-world product demonstration and 100+ patents, Fortera is now operating its first ReCarb® Plant in Redding, California. The plant utilizes the ReCarb® process, a groundbreaking method to manufacture low-carbon cement within the existing production infrastructure. This transformative bolt-on technology seamlessly integrates with current cement facilities, leveraging the entire production framework, from machinery to feedstocks, to ensure a globally scalable solution for sustainable cement manufacturing. The resulting product, Fortera’s ReAct® green cement, is market-ready, meets regulatory standards, and can be blended with or used in place of traditional cement. For more information on Fortera, visit forteraglobal.com.
About CalPortland
CalPortland Company is a major producer of cement, ready mixed concrete, aggregates, concrete products and asphalt in the western United States and Canada. Founded in 1891, CalPortland remains a leader in the industry through its commitment to quality, safety, customer service, technical excellence and environmental leadership. The company maintains its headquarters in Summerlin, Nevada. For more information about CalPortland Company, visit www.calportland.com.
View source version on businesswire.com: https://www.businesswire.com/news/home/20240412693182/en/